AXOR
Celebrating the intersection of technology and craft, AXOR’s commitment to sleek faucet design dates back to 1993. With the recent release of the MyEdition low-profile faucets, longtime brand partner Phoenix Design out of Germany crafted the fixtures in their signature clean-lined, Bauhaus style, with seven interchangeable cover plates and 13 finishes, thanks to AXOR’s FinishPlus program.
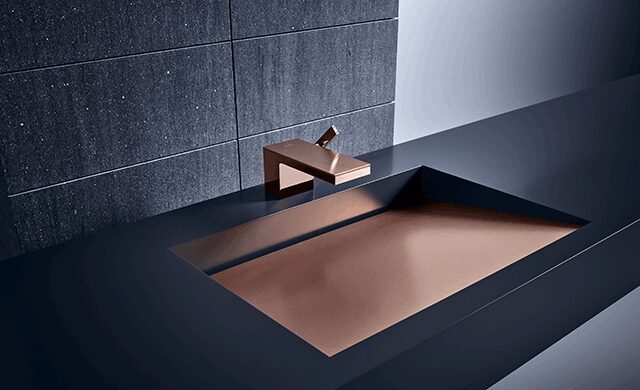
The finished MyEdition faucet, pictured in rose gold from the FinishPlus program, incorporates Hansgrohe’s new PowderRain spray technology, which is a micro-fine mist designed to reduce splashing and enhance the overall experience.
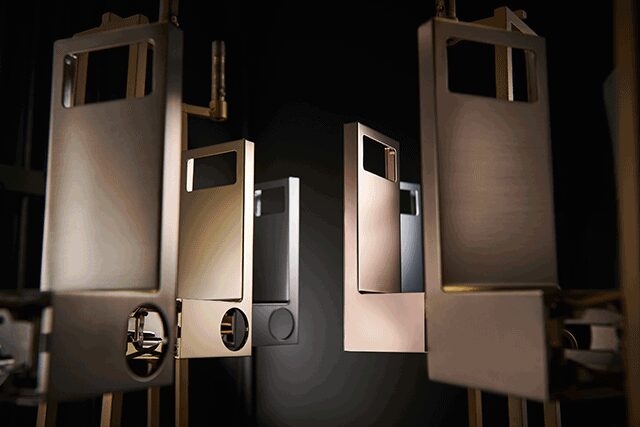
FinishPlus finishes are applied using physical vapor deposition (PVD) technology, in which a coating is applied in a vacuum using steam, bonding the finish to the faucet and resulting in fixtures that are scratch and abrasion resistant. One of the defining characteristics of AXOR is the number of creative colors available, from red gold to black chrome.
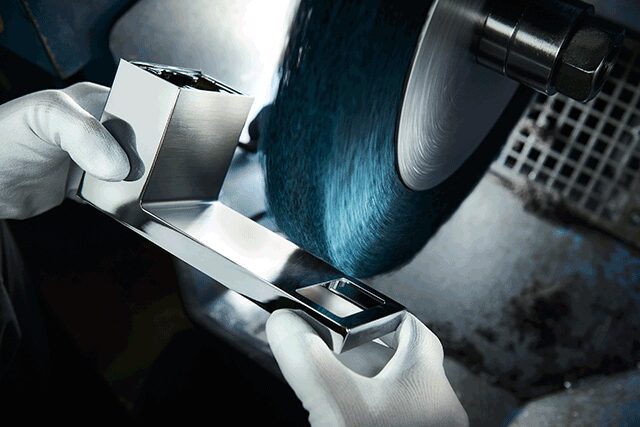
Composed of solid brass, AXOR inspects each faucet component for imperfections. The parts meeting the craftsmanship mark are then hand-polished and finished with the help of a buffing machine.
Fil Doux Textiles
Thanks to a recent partnership with sustainable leather producer Crest Leather, which operates tanneries in Italy, Brazil, and Thailand, Fil Doux now offers leather directly from the tanner to the marketplace. Crest is known for using traditional methods and craftsmanship only found in Italian tanneries, and both companies are committed to more earth-friendly and sustainable practices. During the dying process, for example, Crest has eschewed more traditional wooden drums and started employing metal versions, which use approximately 30 percent less water and chemicals while creating less waste.
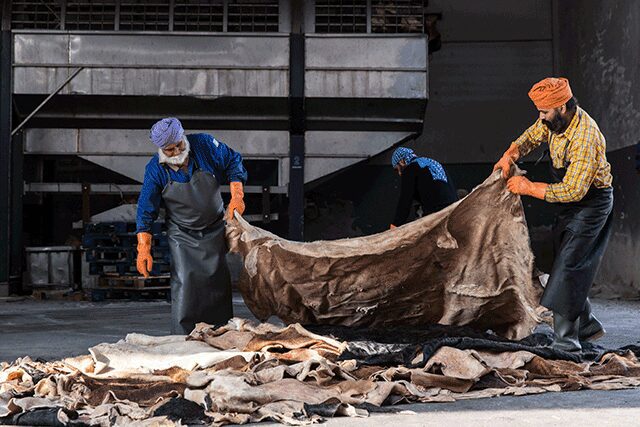
Leather is a valuable by-product of the meat industry, and the global leather industry does not slaughter a single animal. Crest Leather has full control over its raw material selection, ensuring quality of the finished product.
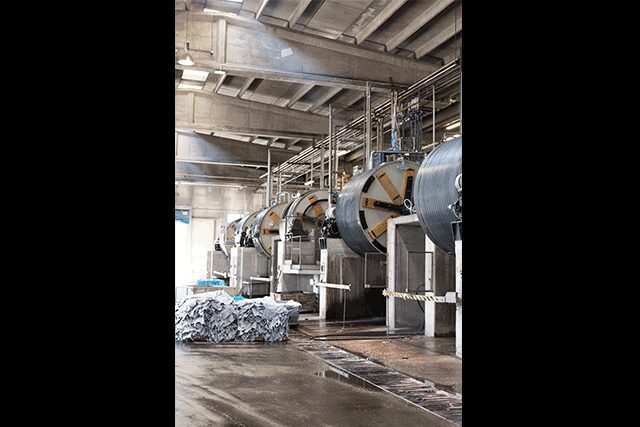
Raw hides turn pale blue after being soaked in a chromium solution—called “wet blue” in this stage of production—and are hung on a conveyer belt, which will take them up to the re-tanning drum.
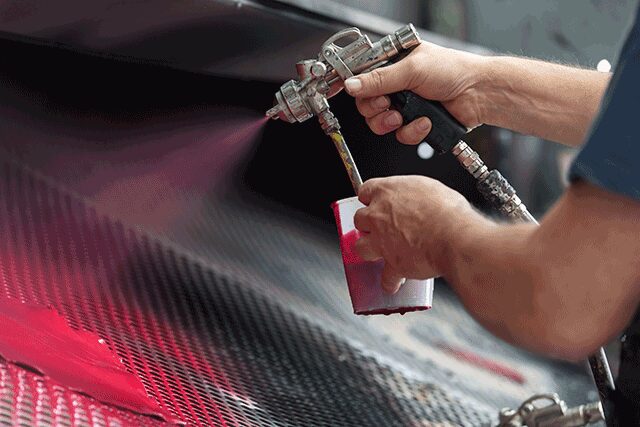
At Crest, an in-house product development team formulates colors and develops new finishes, and sample hides are finished manually and approved prior to mass production.
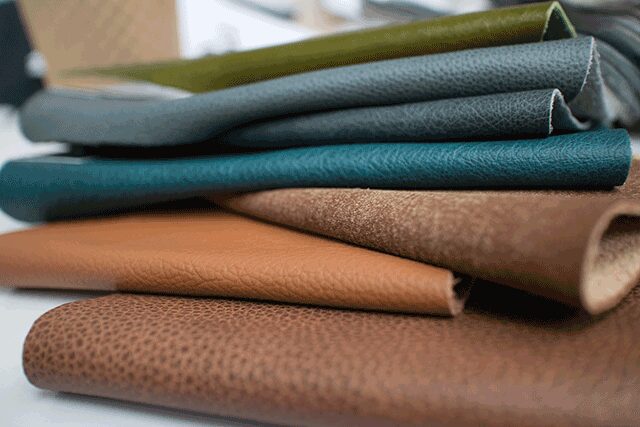
With strict quality control measures in place, the finished collection (done in an array of vibrant colorways) is thoroughly inspected before being shipped out.
Hammerton
Known for its handcrafted steel lighting fixtures, Hammerton has honed its capabilities in both blown- and kiln-fused glass, using tools largely identical to those employed when the trade was established in Italy hundreds of years ago. For these pieces, which are fabricated by artisans in its Utah facilities, Hammerton leverages its metal expertise to create a unique intersection of the two elements. Before production begins, founder and vice president of design Levi Wilson sketches the fixtures by hand before drawing it to scale. One of the company’s latest releases, the Element chandelier, went through a similar process. Made from steel and LED-lit blown glass, it’s available in more than 20 finishes and can be customized in size, glass, and shade options.
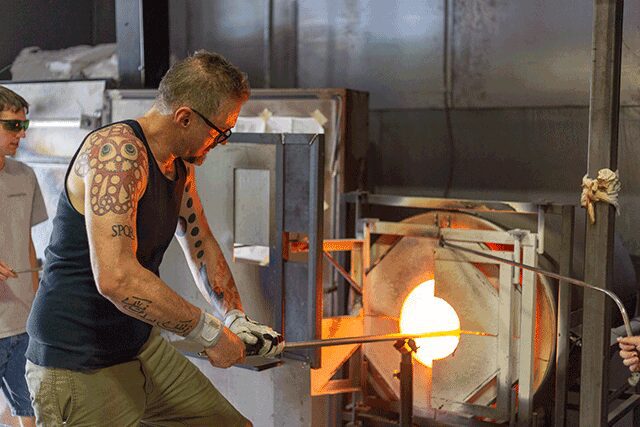
Large blown glass shades, like those found in the Element chandelier, must be reintroduced into the furnace several times during fabrication to achieve the desired shape and form.
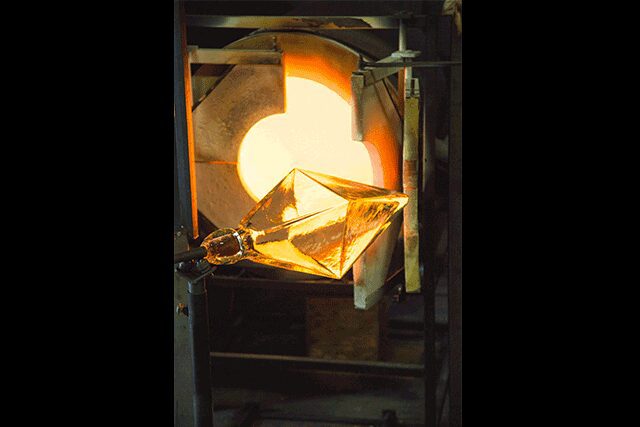
Each blown-glass shade weighs 10 pounds and is created using multiple gathers of molten glass, which are collectively formed and shaped in a custom steel mold that is engineered and fabricated in-house by Hammerton metalsmiths.